Saddled and Spilled: The 2020 Llangennech (Wales) derailment fire

Background
Llangennech is a town and community of 4964 people in southern Wales, located 12km/7.5mi northwest of Swansea and 79km/49mi south of Aberystwyth (both measurements in linear distance) near the Bristol Channel.

The town of Llangennech has a station on the “Heart of Wales”-line, which at that location shares its tracks with the Swansea District Line. The SDW is a double-tracked non-electrified main line opened in 1912 to connect London (England) with the harbor at Fishguard (Wales). Today the line is used almost exclusively for freight services, apart from the section shared with the Heart of Wales line and a handful of passenger services run during weekdays in cooperation with the Stena Line ferry to Ireland. The accident occured just north of Llangennech station, where the SDW diverts to the right as the Heart of Wales line goes straight.
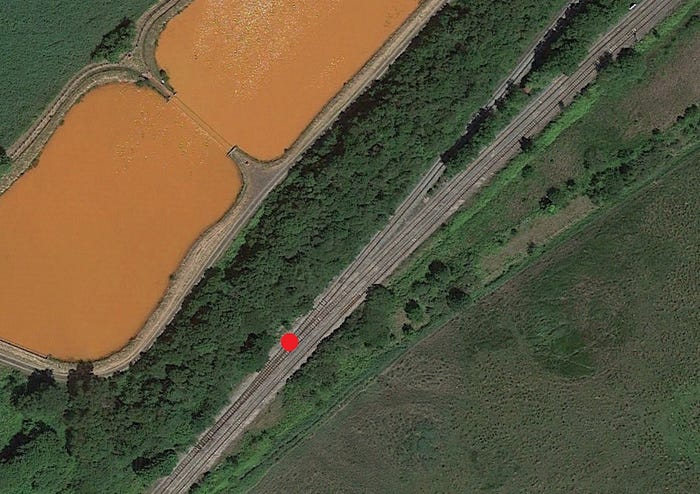
The train involved
6A11 was a freight service from Milford Haven in Wales to Theale in England, consisting of a British Rail Class 60 diesel locomotive (number 60 062) owned by DB Cargo UK and 25 four-axle tank wagons carrying diesel and gas oil. Gas oil is a liquid similar to diesel that is used for heating, often being called red diesel as it is dyed to tell it apart.
The Class 60 is a six-axle diesel locomotive introduced in 1990 to pull heavy freight trains. Each Class 66 measures 21.34m/70ft in length at a weight of 130 metric tons. The locomotives are powered by 145 liter inline-8 diesel engine producing 2311kW/3100hp and enough torque to pull even heavy freight trains at up to 97kph/60mph. All Class 66 were given a name, unit 062 which pulled the train involved in the accident was first named Samuel Johnson (after the famous writer) before being renamed Stainless Pioneer when acquired by DB Cargo UK.
The train on the day of the accident consisted of large four-axle tanker car, types TDA, TEA and TIA. The tanker car that caused the derailment, numbered GERS 89005, was a TEA-type car made in 2001 and had a weight of 101.2 metric tons as it carried 90889l/24000 gallons of diesel. The total weight of the train is listed as 2672 metric tons.

The accident
On the 26th of August 2020 freight train 6A11 has just passed Llangennech station and is approaching the turn-off to follow the SDW eastbound towards the English border. The train is travelling at 61kph/38mph when, at 11:05pm, the third car suddenly derails on the points. A few feet further on the derailed car, still getting dragged along at speed, hits a second set of points, completely forcing it out of alignment. This tears it off car 2, activating the brakes in the whole train as the pneumatic lines are ruptured, but it also derails the following nine train cars. As the back of the train runs into the derailed wagons they push the forward cars in various directions, causing several of them to override each other’s frames or overturn, puncturing the tanks and spilling their cargo onto the hot suspension components. Within moments the devastating spill is worsened by a massive fire engulfing most of the train cars and the full width of the rail line.
The locomotive and first two cars come to a stop 180m/590ft beyond the wreckage, looking towards the back of the train the driver sees the wreckage and the quickly spreading flames. He declares an emergency call to the signal box crew at Port Talbot before closing the brake-valve at the rear of car 2, allowing him to pull the locomotive and leading two cars forward by 400m/1300ft to keep them safe from the fire. Behind him, the towering flames can be seen from miles away, illuminating the night sky as explosions rock the wreckage.
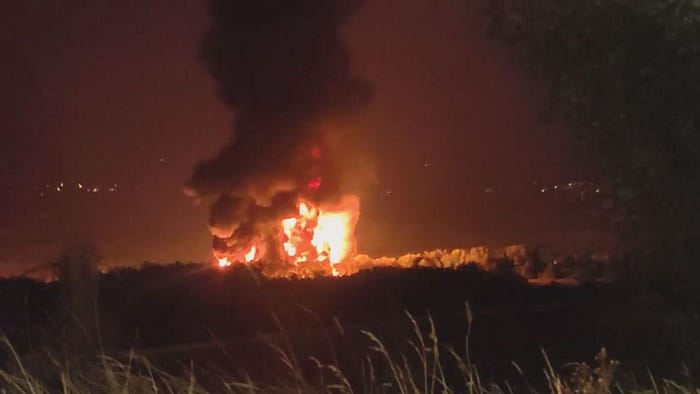
Aftermath
All available emergency responders in the surrounding area are dispatched to the site, within minutes a major incident is declared. Three of the train cars are on fire as responders reach the site, with seven more derailed and expected to fall to the flames. Because of the severity of the fire and the materials involved 300 nearby residents are evacuated from their homes. Responders make the choice to let the leaking fuel burn, aiming to reduce the severity of the spill, focusing on limiting the extend of the fire and protecting the surrounding nature along with the rear train cars. Later evaluations showed that approximately 116000 liters burned up while 330 thousand seeped into the surrounding soil. The incident would become Wales’ most devastating oil spill since a tanker ran aground and punctured its hull near Milford Haven in 1996.

The day after the accident a diesel locomotive is brought in from the south, with responders uncoupling and removing cars 14–25. Investigators started to look into the cause of the accident while firefighters still fought remaining, isolated fires, unable to report the fire extinguished until the morning of August 28th, 33 hours after it started.
With no flaw being found on the locomotive and the data-logger showing perfect behavior by the driver investigators start to comb through what’s left of the freight train once the fire is out. They find that the right hand forward wheel on the third tanker car is severely deformed in a way that can’t be explained by the fire, showing a secondary, false flange along with a 230mm long flat spot on the running surface. The other wheel on the affected axle also shows similar damage.

The damage can only stem from the wheels being stationary as the train went along its route, heating up and slowly getting worn down on the spot that touched the rail. It appears that somehow, at some point, the brakes on the axle became applied unintentionally, stopping the axle from rotating. There was no way for the train driver to notice this, the increase in resistance making barely a difference compared to the weight of the train.
Retracing the train’s journey investigators found that the train passed several signal boxes without the workers present noticing anything odd, but by the time passed the Pen-y-bedd level crossing at 10:46pm, just 18km/11mi from the site of the accident, surveillance cameras captured sparks coming off the faulty axle. Witnesses at nearby Pembrey station also reported an unusual “metal on metal” noise as the train passed through the station, but the signal worker at the station didn’t recall seeing anything out of the ordinary.

Walking back to Llangennech station, just 800m/0.5mi from the site of the accident, investigators spot marks on the rails associated with locked wheels getting dragged along, which is backed up when CCTV-footage again shows sparks coming off the third wagon’s leading axle. The marks continue all the way up to where the derailment and fire destroyed the rails.

Normally modern train wheels have a flange on the inside of the wheel, running up against the inside of the rail and keeping the train on the tracks. When the track curves the outer rail pushes against the flange, forcing the train car to follow the curvature of the tracks. Points work similarly, using a movable section of track to either have the train continue straight ahead or be pushed into a curved route to turn off to the left or right. For this the movable rail lies against the stationary rail, basically “picking up” the wheel and pulling it off the “old” rail by the flange.

The false flange on the third car led to the wheels losing the vital ability to move off the old rail at points, since they now sat against the rail on three sides, rather than two. In exaggerated terms, rather than the sketch above the contact-pattern between the faulty wheels and rails was more similar to a monorail, sitting on top of each rail like a saddle, covering the top and both sides. Perfectly fine as long as the track doesn’t split up, but conventional points are complicated. This, coincidentally, is why monorails have to use entire pieces of track that slide in/out rather than a movable section.


After passing Llangennech station the train first passes a set of trailing points where a crossover from the other track joins the freight train’s track before a set of facing points allows trains to either turn right (staying on the main line) or divert onto the single track Heart of Wales line. At 11:04pm the damaged wheels of the freight train hit the movable section on the trailing points and, unable to move between the movable and fixed sections of tracks, car 3 derails to the left.

Following the derailment of the leading wheelset car 3 was dragged along in its halfway-derailed state for 175m/575ft before it reached the facing points, which were set to keep the train on the main line, heading right. But since the train car had derailed to the left side it didn’t follow the forward part of the train but instead got dragged along the “Heart of Wales” line, to the left. Marks on the track found after the accident indicate that this continued for 8m/26ft before car 3 tipped over, severing the pneumatic connections to car 2 which triggered an emergency stop as the brakes automatically applied.
The destruction of the rails by car 3’s derailment caused several following freight cars to derail as well, running into each other at various angles as the train got out of alignment. Several cars overrode each other’s frame, causing further damage to the tanks and in some cases punctures. Leaking fuel then ignited on hot suspension parts or sparks caused by the derailment, igniting the spilled fluids. During the process of the fire the heat caused excessive pressure in some intact tanker cars at too high an increase rate for the emergency valves, leading to explosions.

This is obviously far from the first time a tanker train has derailed, and there were measures in place meant to avoid the massive spillage. The biggest risk for tanker cars is “overbuffering”, which sees the buffers on the end of the train car climb the frame of the car in front during a rear-ending collision. To reduce the dangers from this tanker cars are fitted with override protections in the forms of upright steel plates standing on the ends of the frame. A 1996 guideline made these mandatory if the distance between the end of the tank and the end of the frame is less than 920mm and the freight car is meant to transport hazardous liquids or gases. However, as in previous derailments, some of the cars moved so much in the vertical direction during the derailment at Llangennech that they overrode the override protection and managed to puncture the tank beyond.

The report does note that the cars involved in the accident had the mandatory override protection, but did not feature recommended further safety-measures such as shrouds and framework to create a crumple zone between the end of the tank and the end of the frame. The recommendation was made after a similar derailment and fire in 2009, along with a recommendation to review protective measures to keep external valves from being sheared off in a derailment. But while the protections couldn’t avoid the spillage and fire the report notes that they did likely drastically downscale the consequences of the derailment, protecting the tanks on several freight cars further down the train.
The question still remained why the brakes had inadvertently applied on the third tanker car, sending investigators back into the scorched remains. At the same time they acquired an identical intact tanker car to compare the wreckage to. For the following we first need a basic understanding of how the brakes on the TEA-type tanker car work. All train cars are hooked up to a pneumatic line from the locomotive, pressurized at approximately 5bar/72.5psi when the brakes are off. Applying the brakes on the locomotive opens the main valve and reduces pressure in the main pneumatic line. The reduction is picked up by the distributor located in the “brake group” on the underside of each car, which then opens the relay valve to let air flow from the individual cars’ onboard reservoirs to the brake actuators on each bogie. The pressure increasing in the actuators moves a piston which operates a system of rods, pushing brake blocks onto the wheels.

The relay valve used on the third car in the train is mounted to the adjacent pipes by means of four O-Rings to create and airtight seal while being held in place by two nuts on threaded rods protruding from the pipe bracket nearby. The valve is connected to a load-sensing valve on each bogie which can differentiate between an empty or loaded freight car, telling the relay valve how much air pressure is needed.

Investigators found the brake group from the third car on the train sitting by the side of the tracks after the accident, having become detached during the derailment. Immediately, several issues were identified:
- The relay valve was only sitting losely on the pipe bracket
- The nuts holding it in place were lose and missing the washers meant to sit behind them
- The mounting studs were only “finger tight” rather than being tightly screwed into their threaded holes
- A 1.5mm gap had formed between the valve and adjacent pipe

A closer examination of the brake group revealed that one of the O-Rings sealing the air passages between the pipe and valve was missing, allowing air to leak out uncontrollably instead of being kept within a controlled passageway. While it could not be proven that the ring had fallen out prior to the derailment investigators noted that the neighboring O-Ring, sealing the connection to the load sensing device, had also moved from its recessed position thanks to the parts being only loosely mounted together. Traces on the mounting-surface of the relay valve indicated that the latter ring had started moving between the surfaces due to the train’s vibrations, travelling upward until it came in contact with two larger O-Rings sealing, respectively, the input from the reservoir and the output towards the actuators. In becoming wedged between the larger rings it forced those into an oval shape, creating an uncontrolled airflow between the valve’s input and output channels.

The air leaking past the valve into the actuators built up enough pressure to apply the brakes on car 3, even if investigators were unable to tell for sure why only leading axle had become completely stationary while the three other axles’ brakes applied at a lesser degree, since too many factors that couldn’t be recreated or researched with certainty play a role in the grip-level of brakes and train wheels.
Originally the brake-system installed on the TEA-Type tanker car had used four M8-bolts on the relay valve. Around 1975 the system was modified, with the upper section being fabricated from aluminum instead of steel. From then on, two M10-bolts were used for installation instead. 10 years later the lower section was updated as well, now also featuring two rather than 4 bolts. However, the four M8-holes were included to enable users of the old design to use the newer part as well. However, they were no longer required to be used. The investigators concluded that the two-bolt design allowed more motion between the surfaces if the bolts were not installed correctly or came lose, making it easier for an O-ring to slip out of position.
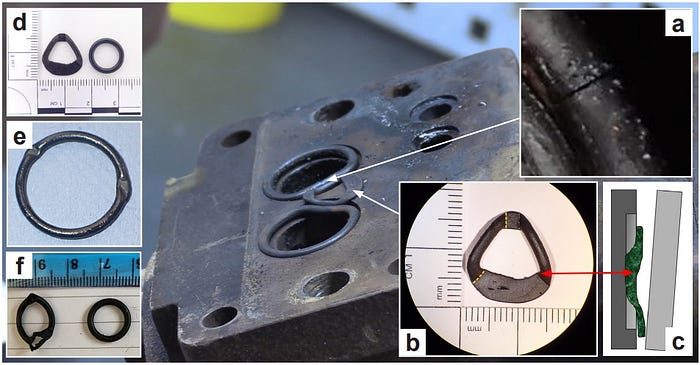
Looking through maintenance records the investigation found that the relay valve had been rebuilt in 2017 and reinstalled, before being removed again in 2019 after the car failed a brake-test upon installation of a new wheelset. The staff at the maintenance facility regularly diagnosed the source of such failures by swapping components between the faulty car and an intact car one by one until the intact one displays the same fault. However, during the 2019 work Touax, owner of the car in question, did not receive the mandatory request to remove valves from the brake-system, indicating that either the relay valve stayed in place or was swapped back and forth without permission before a faulty distributor was diagnosed and replaced. The work was performed by DB Cargo Maintenance, who didn’t document if washers were missing already when they received the car, although they should have noticed the absence when they reinstalled the components with the old hardware.
Furthermore, an October 2019 notice was found that the affected car was “eating brakes”, with a note being made to monitor the issue if it persists. The problem, likely caused by slightly dragging brakes rapidly increasing wear, was apparently not followed up on. Lastly, Tourax failed to provide the car-type’s maintenance manual to the investigation, stating that they couldn’t find it, likely having lost it at an unknown point. This, combined with the fact that a torque-wrench for the relay valve was found by investigators to be broken, led to the conclusion that maintenance workers had neglected to ensure proper installation of the nuts holding the system together, allowing them to gain excessive independent freedom. This led to the O-Rings shifting which in turn led to air bypassing the valve which caused unintentional application of the brakes ahead of the accident.

The report thus traced the accident to negligent maintenance combined with a design-change in the brake-system which made the system more likely to develop the fault that caused the accident. Who exactly had signed off on the faulty repair that led to the accident could not be determined, but the report points out that lose nuts on the relay valve had been found before and Touax had failed to use the chance to control and improve their maintenance guidelines. The investigation thus recommended that more attention is paid to brake systems on train cars, such as paying closer attention to missing pieces like the washers in this case, which indicated faulty maintenance procedures, and maintenance processes. An insufficient fastening of the nuts was only possible because the dedicated torque wrench was broken and workers had apparently chosen to wing it rather than urgently seeking a replacement wrench.
Lastly, the report mentions that the design of axle-temperature sensors along the rail lines (one of which the car passed without tripping it) could be modified so stuck brakes would be detected as well.
The damage at the site was repaired and the line reopened by March 2021. 37500 hours of work had been invested in repairs alone, with 30 thousand metric tons of soil needing to be replaced due to oil contamination. The area of the spill is still easily visible today due to a startling lack of vegetation, and monitoring of the conditions at the site, including soil samples being examined, will continue until at least 2026.


_______________________________________________________________
A kind reader has started posting the installments on reddit for me, I cannot interact with you there but I will read the feedback and corrections. You can find the post right here. Please give it some love, I’m very thankful for the posts being published there.