
Note: This article is by far my longest to date. It wasn’t intended as such, but the more I researched the more information which demanded inclusion seemed to appear.
Background
East Palestine is a town of 4761 people (as of 2020) in the northeastern United States of America, located 123km/76mi southeast of Cleveland and 62km/32mi northwest of Pittsburgh (Pennsylvania) in the state of Ohio, right on the border with Pennsylvania (both measurements in linear distance). In fact, the wreckage and cleanup-zone of this accident ended up spreading into Pennsylvania.

The town lies on the Fort Wayne Line, a mostly double-tracked non-electrified rail line connecting Pittsburgh in Pennsylvania with Chicago in Illinois. The line, which opened back in 1851, is mostly used for freight traffic while also seeing a limited amount of Amtrak passenger services. The line is split between three private rail service providers, with the section surrounding East Palestine being owned by Norfolk Southern Railway, a private rail service provider headquartered in Atlanta, USA.

The Train Involved
32N was a mixed freight train operated by Norfolk Southern, being scheduled to go from a shunting yard at Madison, Illinois, to Norfolk Southern’s Conway Yard facility in Conway, Pennsylvania.

The train was propelled by three General Electric AC44C6M locomotives, with two (NS 4178 and 4224) being at the front of the train while the third (NS 4412) was further back along the train, being remotely operated from the front. This usage, referred to as a Distributed Power Unit (DPU) is typical for the extremely long freight trains commonly running in North America. Fittingly, 32N counted 149 freight cars in length as it approached East Palestine, having been shortened during shunting work at Decatur, Illinois.
The General Electric AC44C6M is a class of six-axle diesel locomotives for freight trains introduced in 2015. They’re constructed by extensively refurbishing GE Dash 9-locomotives (which first entered service in the 1990s). The new locomotives receive new alternating current motors (hence the “AC” name), cabs, hoods and electrical systems while retaining the frame, engine and radiators from the Dash 9. This supposedly delivers improved fuel efficiency and reliability while increasing towing capacity by over 50%. Each AC44C6M measures 22.3m/73ft in length at a service-ready weight of 196 metric tons. The locomotives are fitted with the Dash 9’s four-stroke V16 turbo-diesel engine acting as a 4400hp/3300kW generator (referred to as a Prime Mover) for the electric motors driving the wheels. They can reach 121kph/75mph, although heavy freight services are usually performed at lower speeds. Norfolk Southern is the type’s largest operator, with their 330th unit being delivered in 2025, completing little more than a third of their order.

32N’s configuration and length changed several times during its journey as cars were added and removed, but it consisted of 149 mixed freight cars as it approached East Palestine, 140 of which were loaded. The official report lists the weight of the train (without locomotives) at 17977 tons while measuring 2.84km/1.76 miles in length. For reference, this means that NS 4178 left East Palestine before the rear car entered it as the rail line through town is only 2.69km/1.67mi. Twenty of the train’s freight cars carried hazardous materials, including:
- Chloroethene — Known as Vinyl Chloride, a highly flammable gas with a narcotic effect used in the production of PVC plastic. Burning it produces carbon dioxide and hydrogen chloride
- Butyl Acrylate — A colorless and flammable liquid plasticizer
- 2-Ethylhexyl acrylate — A colorless liquid component used mainly for adhesives
- “Combustible Liquids” like fuel and oil — Very flammable and contaminating
Running in 23rd place on the train was GPLX75465, a four-axle hopper car (a freight car with an open top (or a movable roof) for bulk goods) carrying unknown cargo. The hopper car was manufactured in 1997 for GATX, a private freight car provider, and was running for Braskem America, the US-based division of a Brazilian petrochemical company.

The Accident
32N originated at the TRRA (Terminal Railroad Association of St Louis) yard in Madison, Illinois on the first of February 2023 by being taken over by Norfolk Southern employees. It consisted of 163 mixed freight cars pulled by the three NS-locomotives grouped at the front of the train. The train departed the yard at 10:14pm after a pre-departure inspection and next stopped upon reaching an NS yard at Decatur, Illinois at 6:10am the following day. 55 freight cars were removed from the train, 40 different freight cars were added and NS 4412 was moved back along the train to use it as a DPU in 112th place. This put the train in the configuration it would maintain until the accident. An inspection was conducted on the 40 new freight cars before the train was cleared to depart. The train then continued to Toledo, Ohio, arriving at 1:00pm on the third of February 2023. The stop at Toledo saw a crew change, with the leading locomotive being boarded by an engineer (the US-american term for a train driver), a conductor and a trainee conductor. The engineer had 24 years of experience in his job after starting as a conductor in 1996, while the train’s conductor and trainee conductor had both been hired in 2022. The new crew was briefed by the old crew and conducted a test of the train’s brake system, finding it without fault, before departing for Pennsylvania by 2:15pm.
The biggest risk for freight trains in the USA is so called “Hotboxing”, which refers to the bearing which holds the axle of a train in place overheating which leads to a (potentially fiery) failure. Contrary to road cars the wheels and axles of train cars are one fixed together piece, which is mounted to the train car by an axle stub on the outside rather than having a wheel attached to a hub the way it’s done on cars. These bearings require regular maintenance or they can overheat from the friction between the stationary frame and the spinning axle. Most US rail lines are fitted with Hot Bearing Detectors (HBD), infrared cameras along the rails that point upwards to detect the temperature of each wheel bearing as the train passes over them in order to detect abnormal temperatures before a bearing fails. The approximately 266km/165mi of track between Toledo and East Palestine featured three HBDs, with the final one actually being located at East Palestine.

The HBD at Sebring measured a temperature difference of 3.33°C/38°F between the surrounding air and the 101st bearing to pass over it, which was a bearing on the forward axle of GPLX75465 (“the hopper car” from here). This was the highest temperature difference registered on 32N, and did not raise an alarm. But something was already amiss, because by the time the train approached Salem, Ohio, 33 minutes later a surveillance camera on a trackside business captured a orange light under the hopper car, corresponding to a small fire. The train was literally on fire, but the HBD at Salem only registered a 39°C/103°F difference. This was above NS’ 32°C/90°F limit for an alert, but only triggered a low-level alert to be forwarded to the train control center. There was no alert issued to the locomotive crew, and the HBD-system cannot force a train to stop on its own.

The train eventually approached East Palestine at 8:51pm, travelling at 69kph/43mph under an 80kph/50mph speed limit. The HBD at East Palestine recorded a staggering 122.8°C/253°F difference on the left hand bearing, while the right hand counterpart had registered a harmless 6°C/20°F difference throughout. This temperature difference was finally enough to issue a critical alarm, which caused a speaker in the locomotive’s cab to sound:
“Critical alarm, critical alarm, critical alarm. Norfolk Southern milepost 49.8, track 1 hotbox, axle 101, south rail.”
Such an alarm requires the train crew to stop the train and inspect the wheelset which triggered the alarm. The driver of 32N thus reversed the motors to start slowing the train down as the momentum now worked against the resistance of the motors, a process called dynamic braking. The train barely started slowing down when, at 8:55pm, an airline rupture along the train caused an emergency stop to be triggered without crew input. The leading locomotives came to a stop 38 seconds later, having covered another 354m/1160ft. The crew radioed the dispatcher that they had experienced an emergency which brought the train to a stop, and the dispatcher confirmed that the line would be shut down and trains held or diverted in order to avoid a collision with the stopped train.
Simultaneously, the East Palestine Police Department (EPPD) received an emergency call at 8:56:49pm reporting a derailment, explosion and subsequent fire, soon followed by a consistent stream of further calls about the same incident. The EPPD quickly alerted the local fire department before forwarding the alarm to surrounding municipalities, requesting additional support. The first responders arrived on site by 9:00pm, finding a wreckage spread along over 180m/600ft long of rail line with several localized fires throughout, along with what was later described as a pool of burning liquid running the length of the wreckage. A section of the train was intact and on the track east of the wreckage, followed by a chaotic pile of derailed, overturned and burning rail cars, followed by another short section of intact train cars and the third locomotive sitting west of the wreckage.

Initial Aftermath
The deputy fire chief (his superior was on leave at the time) took command of the site, setting up a command post southeast of the wreckage and ordering his men to start hosing the burning rail cars down with water. However, he soon found that this practice was insufficient to suppress the fires. The emergency dispatch center called Norfolk Southern’s dispatcher at 9:04am, requesting information on the configuration, length and cargo of the train. The employee who picked up the phone said he would gather the information and call back, but there is no record of him ever calling back.
The conductor of 32N had just prepared to step off the locomotive to walk along the train when he was informed of the fire on the train, leading him to retreat to the cab due to fearing the hazardous cargo on the train. The engineer received permission to separate the leading locomotives from the train by 10:15pm, aiming to remove them (and their considerable fuel load) from the proximity of the fire. The two locomotives were thus uncoupled and moved 1.6km/1mi east of the blaze. Another movement around 11:40pm would see them end up 42km/26mi from the fire.
The emergency dispatch center continuously attempted to extract information from Norfolk Southern between 9 and 10pm while also coordinating an evacuation of residential buildings near the wreckage. An emergency notification system was used to urge residents within a mile of the site to shelter indoors.

Norfolk Southern eventually provided information on the train to the Columbiana County Emergency Management Agency (CCEMA), who had requested the information after East Palestine’s emergency dispatch center kept being ignored. Someone with Norfolk Southern then also called the local fire department, telling the deputy fire chief about two of the hazardous materials on the train, namely benzene and vinyl chloride (VCM). A firefighter with the responding East Liverpool fire department managed to access a copy of 32N’s cargo paperwork through a specialized phone app while en route to East Palestine, arriving on scene just before 10:00pm. He was travelling with his fire chief in a command vehicle well ahead of his department’s trucks, and incompatible radio systems between the two fire departments also meant the little help him and his fire chief could provide was slowed down by having to be forwarded via the command post. The two men determined which freight cars were within the fire, and which one of those were carrying which cargo. They considered the VCM to be “the worst material present”, and, being unable to quickly identify the burning tank cars carrying the material, recommended a 1 mile evacuation radius. The specialized Beaver County hazardous material response team arrived at 10:30pm, and the head of the crew was everything but impressed by the conditions on site, describing the command post as almost as much of a train wreck as the literal train wreck next to it, pointing out poor command structure and a high amount of general chaos.
A one mile evacuation radius was ordered by 11:00pm, just as Norfolk Southern’s own hazardous material personell arrived at the site. A contractor sent by Norfolk Southern later recalled observing the lengthy pool burning south of the rail line, distinctly smelling that Butyl Acrylates were burning. The specialized responders focused on determining which materials were within the fire, which was made extremely difficult by the poor visibility (darkness and heavy smoke) along with information/warning placards on several rail cars having been destroyed (more on that later). Due to the sustained risk firefighting was suspended by midnight, with responders moving to the edge of the mile-wide evacuation radius. The pool was observed continuously setting fire to various cargo spilling from cars along the wreckage while also igniting gasses as the overpressure vents on tank cars released their cargo in order to avoid explosions.

Aftermath
Firefighting efforts continued on a small scale along the edge of the wreckage, staying clear of the center of the wreckage. Drones and helicopters were used to observe the burning freight cars near the center of the wreckage, particularly five tank cars carrying VCM and one carrying Isobutylene (a flammable gas in the same hazard-class). As the fires died down and became more localized the NS started to consider removing the VCM from the still-intact tank cars in the wreckage, either by a controlled burn through an inserted pipe or by welding a nozzle onto the tank car and drilling through the wall of the tank, effectively replacing the damaged fittings that prohibited regular unloading. The planning came to an end when one of the tank cars (OCPX80179) had it’s emergency release valve (PRD) activate in an unusual way the morning after the derailment, shooting a large column of fire into the air for over an hour. Usually, the release is meant to be more subdued, slowly releasing the gas at a limited pressure. The excessive activation indicated that a chemical reaction had taken place within the tank car due to the prolonged exposure to fire, making the alternative (installing a new fitting) unreasonably dangerous. But the tank car also couldn’t be left as is, since rising temperatures inside indicated climbing pressure, and the faulty PRD could not be trusted to avoid an explosion which would send shrapnel into the surroundings.

The Federal Railroad Administration considers “Vent and Burn” the last resort to remove cargo from a damaged tank car, only to be used when all other options are unreasonable or have been exhausted. The technique sees a prepared pit being dug at the lowest end of the rail car before explosives are used to breach the tank at both the highest and lowest point. Gases and vapors escaping at the highest point are burned with a flare in order to neutralize them, while the pit is used to collect (and burn) draining liquid cargo.
A contractor (SPSI) sent to the site by NS proposed venting and burning all five VCM tank cars, even though not all five indicated the same issue as OCPX80179. He argued that the cars were close together, with venting and burning resulting in a fire that could further damage the other tank cars if they weren’t vented too. A lengthy discussion ensued, also involving the company who had chartered the tank cars and local politicians, while the temperature of the tank cars in question was continuously monitored. During the same time, barriers had been set up on two local rivers as leaking cargo had started getting into those creeks. It was eventually decided that a vent and burn on all five VCM tank cars would be conducted. Preparations saw the pits being prepared, the evacuation-radius increased by 50% (from a 1 mile radius to a 1x2 mile rectangular area) and charges along with flares to ignite the gas and pits were set up on the tank cars. Planned detonations rang out at 4:37pm on the sixth of February, with the burning VCM resulting in an enormous black cloud forming over the site.

Firefighting efforts around the site largely concluded the same day, now that responders could properly access the site as the risk was considered handled. Wreckage clearing began the next day, with NS sending a first train through the site on the other track (which had only suffered minor damage) at 4:46pm on February 8. It must have been a bewildering sight to see freight trains crawl through one’s hometown so soon after a derailment while you weren’t allowed to be in your home due to safety reasons.
Local authorities started reducing the evacuation-radius about an hour after the first train had passed through, claiming that air quality readings were showing any harmful materials in the air to be below the relevant levels. This happened as people in neighboring counties still reported a “chemical smell” in the air, and the officials at Youngstown (32km/20mi north of East Palestine) advised residents to stay indoors due to air contamination. The evacuation order was fully withdrawn on the ninth of February. Tests conducted by the University of Wisconsin would later show that the fire, especially the vent and burn, had propelled toxic chemicals into the atmosphere in a way that caused pollution in 16 US-states, covering an area of 1.4 Million km²/540 thousand square miles. It took two weeks for some pollution-levels to return to normal.

The Cause
The NTSB had started examining the wreckage in order to find the cause back on February 4th, quickly zeroing on hopper car GPLX75465 as it had tripped the alarm just ahead of the derailment. They got a big hint when they accessed the still smoldering car on the eastern end of the (as the report puts it) derailment pile, namely that the four-axle car only had three axles. The missing axle was found nearby, showing fire damage and missing the left hand bearing. A search around the outer part of the wreckage (steering clear of the burning tank cars) turned up several pieces of the missing bearing on the opposite end of the wreckage, with the investigators recovering most of the bearing assembly. Some components, such as part of the rollers, the backing ring and an inner seal ring couldn’t be found. The investigation noted that the journal, which is the part of the axle stuck within the bearing, wasn’t exposed to fire, showing rust on the outside and intact metal where it would be within the bearing.


A contractor from the manufacturer disassembled the recovered pieces by April 2023, finding that the bearing’s grease seal was missing and the steel components that were recovered showed extensive damage. These included signs of past melting of the metal, galling (material transfer by rubbing), abrasive wear (as if a part had been attacked with sandpaper) and plastic deformation of metal components caused by external or internal forces. Most of the damage found was indicative of a severely overheated bearing giving out under the load of the car its axle carries, with the found oval deformation of the metal bearing being a possible consequence of excessive overheating weakening the metal so far that the weight of the train car presses it out of shape.

The investigators found scraping on top of the southern (right hand) rail ahead of the wreckage site, expanding for over 425m/1400ft. The degree and shape of the scrapes indicated that something rather heavy and sturdy was being dragged along the rail at that point. The sleepers (the wooden or concrete beams connecting the rails, also called crossties) further showed groves which were consistent with a derailed train wheel’s flange running along them, cutting into the material as it went. The combination of the damages and their extension matched the scenario of a derailed rail car being dragged along without forcing its train out of line. However, especially the rail-top markings were only possible if something like the frame of a bogie was sitting on the rail, which can only happen if the wheel is missing.

A bearing failure can cause ejection of an axle, which would create a severe misalignment (and derailment) within a very short distance, but the damage found at East Palestine indicated a different kind of failure in which a bearing fails to maintain smooth rotation of the axle within it but still keeps the axle-stub contained, leading to the friction generating excessive heat. This can cause the axle to heat up and weaken to the point of shearing off between the wheel and the journal (“burn-off”). In that case one side of the bogie can touch the rail, while the other is still held up by its wheel. The look of the damage would be comparable to the wheel studs failing on a car, jamming the wheel into the wheelhouse rather than ejecting it.
The investigators concluded that the L1 bearing (which runs on the right hand side of the train car, confusingly) failed as the train approached East Palestine, leading to a burn-off which generated the heat to set off the HBD at East Palestine and separated the wheel from the journal. The train car’s leading axle thus lost it’s guidance along the rail on one side, keeping the train car somewhat aligned with the train as the left hand wheel ran on the rail and the right hand wheel bumped across the sleepers. This incredibly unstable balance eventually failed, causing a derailment and ejection of the bearing-pieces. This then caused a separation of the train’s pneumatic through-line which triggered an emergency stop. The derailed hopper car continued to be dragged along on three axles for a significant distance before separating from the train in front as well, ending up at the eastern end of the 38-car pileup that ensued behind it.
The cause of the bearing failure couldn’t be determined with precision, since the condition at recovery didn’t provide a clear image of it’s pre-failure condition. Bearing failure in the way it happened at East Palestine usually occurs from insufficient lubrication, but the investigation couldn’t determine if insufficient lubricant had been provided during the last overhaul or if maintenance crews had failed to notice a gradual leak of lubricant which left too little in the bearing.

Examination of the burned rail cars revealed that several of the 27 derailed tank cars had suffered punctures during the derailment, most of which occurring most likely when they rammed the train car in front of them or were rammed from behind. While the source of the igniting spark couldn’t be determined the first train car to catch fire was UTLX205907, a DOT-111 tank car carrying Butyl Acrylates, a flammable liquid which has a flash point (temperature at which it will provide enough vapor to ignite) of just 40°C/104°F, the lowest of all released materials. DOT-111 is a construction standard for four-axle unpressurized tank cars introduced in the 1960s. The type, which makes up over 2/3 of US tank cars, has no standard requirement for additional protective measures, including no heat shielding and no impact protection beyond the standard buffer and frame layout it shares with most freight cars.
The large pool which was witnessed burning in the hours after the derailment was likely fueled by UTLX205907 and two other DOT-111 tank cars who lost their load through punctures and whose cargo was met with the fire providing sufficient heat for higher flash points. The burning pool then provided the flame to set other cargo ablaze.

The report notes that the train’s DOT-111 tank cars which lost their cargo almost exclusively did so by suffering punctures during the derailment, while the three DOT-117 tank cars which derailed remained intact, as did the five DOT-105 tank cars carrying VCM. The outdated construction of the DOT-111 standard, inferior to the DOT-117 and -105 thus played an integral role in the outcome of the derailment, as more modern tank cars would’ve likely resisted the suffered impacts without puncture and thus wouldn’t have caused a fire. We will get back to the DOT-111-issue later, but a bigger question mark came up from the safety measures. The rail line was fitted with HBD-systems, so why did they not recognize the heat until it had been so intense for so long that the axle gave out?

The HBD at Salem, Ohio, recorded a temperature of 39°C/103°F above the ambient temperature. This was above NS’ 32°C/90°F limit for an alert, but remained below the 77°C/170°F threshold for an alert in the driver’s cab. The reading thus only produced a “non-critical” alert for an abnormal reading to show up on the screen at the train control center, which demanded that the suspicious bearing’s readings be observed through the following HBDs. Not only was this impossible as the train derailed while passing over the following HBD, the alert also wasn’t even seen by the employee on duty at the center since he was occupied with higher-priority alerts at the time.
The NTSB examined the system at Salem and found that it was set up to take temperature readings on the inside of the rail, scanning the bearing cup on the inside of the wheel from below. Surveillance cameras showed that the heat on the outside of the bearing had risen high enough to set lubricant or other flammable materials ablaze as the train reached Salem, but the material, mass and construction of the bearing meant that the part of the bearing scanned by the camera had not yet heated up as much, aided by the steel wheel shielding most of the radiating heat. This resulted in a bearing that was quite literally on fire to report as only “abnormal”, only to give out less than 32km/20mi later. A calculation resulted in the assumption that the outside of the bearing was at no less than 123°C/253°F when it passed over the HBD at Salem, which unfortunately was on the wrong side of the rail to notice.

The position of the HBD cameras is always a compromise, as a bearing failure can be hidden from the sensors inside the rail (as happened here) while a sensor outside the rail may have the bearing obscured by parts of the train car, which would lead to inaccurate readings as well. HBDs with sensors on both sides of each rail, which may spot a failing bearing sooner, exist but are less common.
The positioning of the HBDs along with their spacing and the different thresholds did not create an opportunity for the control center crew or the train crew to notice what was about to happen any sooner, a problem escalated by a reading above the first threshold only being a non-critical alert even though a failed bearing was known to have possibly catastrophic consequences.
The NTSB proceeded to host a hearing attended by representative of the NS, where they asked them to explain their strategy surrounding HBD systems. The NS’ assistant vice president of signals and communications testified that their thresholds and alarms are based on the AAR’s (Association of American Railroads) standards and classifications around bearing conditions. However, a representative of the AAR subsequently explained that their definition of an overheated bearing is not based on the operational safety of a bearing but on the repairability of a rail car with bearings in that condition, more specifically on the billing for a repair. The railway operators then pick their own thresholds based on a balance of safety, repair cost and avoiding unnecessary stops. That means that the guidelines from the AAR used by the railroad companies not only create uneven thresholds depending on who owns the section of track a train happens to be on, but are also based on damage caused inside a bearing only to be applied to a process measuring the outside. The HBD systems in use are an improvement of operational safety, but, in simplified terms, leave a lot to be desired.
In summary, the HBDs along the rail line were unable to create a sufficient warning as they had been set up on non-ideal guidelines, which caused a bearing to fail before the crew could stop the train. The failed bearing led to the derailment of the freight car due to it suddenly loosing its axle-attachment on one side, causing a derailment which took out a significant part of the train, involving several tank cars. Some of those tank cars, which were carrying flammable and/or hazardous cargo, then punctured and sparked a fire, causing the failure of further tank cars.

The Fallout
Normally, this point would be the end of it. The cause was determined as far as could be, a report was written up by the NTSB, and the site was cleared with the track being repaired. But the derailment at East Palestine, as it would turn out, had somewhat ripped the curtain back on deep-rooted issues in US rail traffic, particularly freight rail.
Waiting for another Lac-Mégantic
As it quickly turned out DOT-111 tank cars had a history of losing their cargo by puncture in derailments, causing fires:
- A freight rain containing 19 DOT-111 tank cars derailed in Cherry Valley, Illinois (USA) on June 19th 2009. All 19 tank cars derailed with 13 breaching as the wreckage caught fire while 324 thousand gallons (1.2 million liters) of Ethanol were released uncontrollably. The derailment and following fire caused the evacuation of 600 homes, claimed a life and injured nine people. The NTSB recommended that DOT-111 cars intended for hazardous materials be upgraded to newer standards through additions like heat shields, tank jackets (an additional layer of steel around the tank) and thicker tank walls. It was also recommended that the release valves on the bottom of tank cars be protected against impact damage, since they could presently be torn off in crashes which led to material being released.
- A freight train consisting of of 72 DOT-111 tank cars carrying cruide oil derailed in Lac-Mégantic, Canada, on July 5th 2013 after running away unmanned, making its way downhill into town where 63 tank cars derailed, releasing 1.6 Million Gallons (6.05 million liters) of the highly flammable cargo. The escaping oil ignited and turned the town’s downtown area into an inferno which claimed the lives of 47 people. The NTSB reiterated their suggestions from the Cherry Valley derailment, recommending an upgrade of DOT-111 cars, primarily those carrying highly flammable cargo, to the DOT-117 standard which offers higher crash safety.
- 13 rail cars carrying grain derailed at Casselton, North Dakota (USA) on December 30, 2013. The derailed cars reached into the neighboring track where they were struck by an oncoming 104-car crude oil train. 20 DOT-111 tank cars derailed with 18 being punctured which released almost half a million gallons (1.9 million liters) of crude oil, starting a fire. The fire was escalated in severity by a pool of burning liquid causing the failure of non-punctured tank cars (as their tanks melted through).
- 27 DOT-111 tank cars with crude oil derailed at Mount Carbon, West Virginia (USA) on the 16th of February 2015. The tank cars had upgraded crash safety but no heat protection, leading to an initial puncture of just 2 tank cars providing a burning pool which caused the failure of another 13 tank cars.

The AAR introduced safety upgrades for new DOT-111 tank cars back in 2011, including thicker walls and a 12mm heat shield, but the new construction standard didn’t involve upgrades to existing cars which were allowed to continue service unimpacted. The Federal Railroad Administration (FRA) and their Canadian counterpart Transport Canada (80% of Canadian tank cars are DOT-111) announced a switch to the DOT-117 standard as a minimum requirement for flammable cargo in 2015, aiming to reign in the risk posed by the old design. DOT-111 cars for flammable cargo would have to be upgraded or retired by May 2025. The new standard is required for highly flammable cargo, any group of 20 or more tank cars carrying flammable liquid or when a tank car runs in a train with 35 or more tank cars carrying flammable cargo spread out over the length of a train. The new requirement was largely welcomed by rail companies, with most opposing voices coming “from the trackside” remarking how the focus should be on avoiding accidents rather than moderating the outcome of an accident.
So, finally, there is going to be an end to (almost) endless trains carrying flammable liquids or gases in these outdated tank cars, even if it is a very slow and gradual end. The risk posed by the old tank cars was well known even ahead of the disaster at Lac-Mégantic, and yet it took over 10 years after that tragedy for the tank cars to begin being phased out. With the amount of flammable cargo bumbling through towns and cities across the USA day after day one could say that it’s lucky that North American railroads are in a way still waiting for another Lac-Mégantic, now with hope that the type might be retired before it occurs. It is an interesting note that the end is actually welcomed by most railroad companies, as one may expect that they would very much like to hold on to existing rolling stock due to cost of replacements or upgrades. But even if their primary motivator is the cost and image loss of catastrophic derailments it is a good thing that they’re not resisting the switch to newer and safer designs. If only that didn’t have taken quite so long.

Urgent information not urgently available
Federal regulations in the USA require that standardized placards must be attached to both ends and both sides of a rail car carrying hazardous cargo. These square, brightly colored stickers display the main risk posed by the cargo along with a log-number that allows identification of the cargo. These stickers are meant to allow responders after an accident to quickly identify the contents of different rail cars, which may externally look the same (especially if they’re on fire). The placards can be made of tagboard (a type of cardboard), different plastics or metal, and regulations demand that they remain effective after 30 days of uninterrupted exposure to any weather. However, the guideline does not demand any specific resistance to heat and fire.
Guidelines for responders specifically instruct to stay at a distance, if possible by using binoculars, until they can decipher the placards and tell what cargo they’re faced with. Both the firefighting and cleanup effort at East Palestine were significantly slowed down as firefighters (and later cleanup-crews) couldn’t tell what cargo a tank car contained as the placards had often burned or melted into unrecognizability.

The second way responders could find out what a freight car contained was to request the information from the rail operator, which was done at 9:04pm, 8 minutes after the emergency was declared. The contacted dispatch center in Atlanta, Georgia, did not provide this information at the time and it took almost an hour for information on the cargo to be mailed to the CCEMA director as he was en route to the site. The on-site commander was informed of benzene and VCM being aboard the derailed train via phone call around the same time, from which point on the information gradually spread among responders. This delayed the establishment of a recommended evacuation zone until 11:00pm. The hour between the first request and any information being provided was already a needless delay, further escalated by incompatible radio systems making it difficult to inform all responders on site in an organized matter. This left responders and residents close to, to them largely unknown, hazards for much longer than necessary.
The NS reacted to the criticism from the NTSB by upgrading their emergency response systems, integrating it into the RapidSOS online system which can provide the information automatically almost instantly as soon as emergency services are notified of a derailment. It’s unknown why the NS failed to respond sooner to the request after the derailment at East Palestine, with the reaction time being comparable to a 2005 train crash at Anding, Mississippi, where the printed out information stored aboard the train was lost to fire and the railroad in that accident (Canadian National) had relied on responders or crew members retrieving the printout from the cab in case of an accident. It was eventually provided in that case by surviving crew members listing cargo from memory, had they died in the collision (as did four of their coworkers), or been too injured to provide information, the response may have been slowed down further.
The aftermath of that accident had led to a demand that railroads must have the ability to immediately provide emergency responders with accurate information about the hazardous cargo on a freight train, regardless of train condition or crew survival. 18 years later, East Palestine showed that at least some rail operators had failed to meet the demand.

Scorched Air
A much bigger issue turned out to be the handling of freight cars in the wreckage that specifically weren’t on fire after the derailment. Namely, the five tanker cars carrying VCM. Employees of the SPSI went around with infrared thermometers, examining the five tank cars. They found that one of them, OCPX80370, at times showed significantly increased temperatures. This, along with OCPX80179 showing a violent release of gas from its emergency release valve (as noted earlier in this article), raised concerns that their cargo might undergo polymerization, a chemical process which produces significant heat, increasing the fears of an explosion (and further fires). Polymerization of VCM would also create a solid material, which could settle in the release valves and result in them being stuck. And without a release valve, in simplified terms, a tank car exposed to heat turns into a bus-sized pipe bomb. The NS’ representatives on site proceeded to push heavily for the vent and burn procedure to be conducted on the five cars, constantly reminding other responders of the possibility of a catastrophic tank failure (read: explosion). However, Oxy Vinyls, the company who had contracted the tank cars and owned the cargo, did not agree with the NS’ opinion when going off the same information.
Oxy Vinyls’ onside representatives kept charting the temperatures from repeated measurements and found temperatures on a generally stable or even declining trajectory, interrupted by occasional spikes. A polymerization, as they later explained to the NTSB, would instead show a rapid and consistent increase in temperature which wouldn’t stop at random.

Oxy Vinyls’ representatives shared these findings on a conference call with coworkers in Dallas, Texas, concluding that in their expertise no polymerization was taking place. They met with SPSI-representatives at 7:00pm on the fifth of February, by which point preparations for the vent and burn had begun. The meeting did not change the course of action, and neither SPSI nor NS shared the information received from Oxy Vinyls with the command post, to which Oxy Vinyls’ representatives had no direct contact. According to the NTSB the situation on site was as such that the incident command might not even have known that Oxy Vinyls had experts on site to consult, relying on NS and SPSI to provide them with the best possible information while those neglected to forward Oxy Vinyls’ information. Oxy Vinyls’ technical manager later testified at an NTSB-hearing that he trusted that his company’s input was being forwarded, and that it didn’t cross his mind that they wouldn’t do such an obvious thing.
Representatives from the NS and its contractors told the incident commander during a meeting on the sixth of February that temperatures exceeding 153°F/67°C would result in an uncontrollable polymerization. They further explained that the site would have to be abandoned, making a vent and burn impossible, if the temperature passed 150°F/65.5°F. These given values do not correspond with the information provided by Oxy Vinyls. Furthermore, while the NS urged for a vent and burn to be ordered within 13 minutes by giving a 3:00pm deadline due to atmospheric conditions, OCPX80370 measured 126°F/52°C on a declining trend.

The incident commander later testified that he trusted the information he was provided and was (understandably) worried about train cars full of toxic cargo exploding, so he eventually agreed and ordered the vent and burn procedure to be conducted. Several delays pushed the initiation of the process to 4:37pm, already indicating that the deadline wasn’t as definitive as implied, but by that point the decision was made. The NTSB severely criticized the NS for their behavior ahead of the procedure being conducted, from failing to forward important information provided by on-site experts to compromising the decision-making by creating unnecessary urgency. Fittingly, the report advises Oxy Vinyls to create a system that ensures incident commands in future cases receive their information regardless of the train operator’s behavior.
The vent and burn had been the main source of toxic gasses being released into the environment after the derailment, alongside the burning of plastic cargo and leaking oils which contaminated the water and killed thousands of fish in local creeks. Investigators from the NTSB examined the five tank cars after the vent and burn had finished, finding damaged and in some cases clogged release valves, but no evidence of polymerization. The unusually violent activation of OCPX80179, they concluded, was not caused by violently excessive inside pressure through polymerization, but due to a faulty valve. Effectively, the vent and burn procedure had been unnecessary, significantly worsening the pollution in the area for no objective reason.

The NS obviously rejected the claim, explaining that the other options like attaching new fittings to damaged tank cars to unload/move the cargo were too dangerous, requiring work close to possibly faulty train cars still holding dangerous cargo, including the ones they would be working on. They argued that the vent and burn was the only option which didn’t pose unnecessary risk to workers, which was also why all five tank cars underwent the procedure instead of just the one (OCPX80370) which showed elevated temperatures. This was further justified by saying that performing the vent and burn on one of the tank cars put other tank cars in danger from the detonations and fires. However, a derailed tank car carrying Isobutylene (a flammable gas in the same category as VCM) was sitting closer to OCPX80370 than the other four VCM cars and was left alone during the vent and burn, having its cargo transferred without incident at a later point.
Lastly, the report explains that the NS ignored the most obvious option given by the provided information: Waiting. Only one of the five tank cars had seen a relevant increase in temperature, and it was on a clearly declining trajectory, so they could have just waited for temperatures to reduce further before assessing the condition of each tank car. They did that with the Isobutylene tank car, examining it and eventually finding it to be structurally intact, but the vent and burn procedure, which involves blowing two holes into the tank and setting a fire, took away this option for the five VCM cars. The fact that OCPX80370 was initially resting against a burning hopper car, which would have aided in the temperature increase, seems to have been largely ignored simply due to the fire being out by the time measurements were taken.

The NTSB collected the five VCM cars’ PRD-systems during wreckage removal for bench testing at a laboratory. One of the systems was missing significant components and had partially melted, but the other four could be tested. Three of the four other PRDs began to leak or even open well below their supposed activation-pressure, while the valve from OCPX80370 was stuck closed and wouldn’t release any pressure by the time the test was aborted for safety concerns, marking it as still closed at 18.9bar/275psig (1.7bar/25psig above its activation-point). Disassembly found the internals of all four valves to be damaged, showing corrosion, bent/permanently compressed springs and parts stuck together. However, the report notes that the valves were in storage for six weeks between the derailment and the tests, and since they were recovered without cleaning them this time may have worsened the condition of the valves. Exposure to hydrogen chloride, which is produced when VCM is burning, during activation and the vent and burn likely also deteriorated the valves from their pre-derailment condition.
Some of the five tank cars had been fitted with aluminum components such as protective covers, which were made out of steel on other tank cars. These had melted and partially seeped into the valve systems before hardening again, but the condition of the valves during testing did not allow for a certain determination that the switch to aluminum components contributed to the release of hazardous materials. More interestingly, none of the valves showed any PVC-residue, which confirmed that no polymerization had taken place.

Regulating Itself
The new safety-standards introduced in 2015 created the label of a High-Hazard Flammable Train (HHFT) in the aftermath of the Lac-Mégantic derailment and fire (mentioned earlier). These HHFTs are specific trains with especially high amounts of hazardous, specifically flammable cargo, which were thus subjected to more regulation to increase their operational safety. An HHFT-train was any train carrying 20 or more tank cars with a Class 3 flammable liquid in a row or more than 34 spread out throughout the train. Examples for Class 3 flammable liquids are fuel, ethanol and fuel oil (diesel), all liquids with a flash point of less than 60°C/140°F. The NTSB had criticized the excessively narrow definition, excluding a number of hazardous materials, but was ignored. The FAST-Act (“Fixing America’s Surface Transportation Act”), signed into law by the Obama-administration in December 2015, set the definition in stone and made changes to it almost impossible.
The shortcomings of the definition were on full display at East Palestine. 32N wasn’t an HHFT, but its DOT-111 tank cars with flammable liquids on board ruptured during the derailment, causing fires which then led to other tank cars releasing flammable gasses through their PRD-systems due to the heat. However, those gasses were class 2, not subjected to the HHFT regulation, even though they caused the kind of a cascading failure and cargo-release HHFT-rules were meant to prevent. A revision of the HHFT to include more flammable liquids and any flammable gasses would be sensible, but would have to make it through the notoriously irrational US political system as the PHMSA (United States Pipeline and Hazardous Materials Safety Administration), the entity which created the guideline, lost the ability to edit it when the FAST-act was signed. In fact, only one significant edit was done to the Act, when the Trump-Administration removed a requirement for improved braking systems from it in 2017. This change was not undone by the following administrations as of February 2025. The shortcomings of the current standards, specifically the HHFT, are so well and widely known in the industry that a lot of rail workers have nicknamed trains with high amounts of flammable cargo “bomb trains”. Not a term you really want to hear referring to something that is travelling all over the country day and night. The term is by no means exaggerated, as just 22 train cars full of LNG (liquid natural gas) hold the equivalent of the energy released by the atomic bomb at Hiroshima.


Norfolk Southern is considered an industry leader in North-American railroading, frequently breaking records for both train length and train weights, while also having cut down its workforce by nearly 30 percent in the 2010s. To be fair, that last part does not make it stand out among its competitors. However, this cut in personell wasn’t performed the way one may expect. They didn’t improve safety-systems and thus got rid of two-man locomotive crews, going to single-man crews like most of the world. They cut staff across the board, affecting locomotive crews but also maintenance and office workers. This is while the trains keep growing (and many cars age), producing a somewhat contradictory image and increasing risks. They also consistently invest over a million Dollars per year in lobbying the national congress, federal agencies and the White House on issues mostly surrounding railroad safety and staffing, with filings showing 20.7 Million USD spent on a federal level between 2013 and the 2023 derailment at East Palestine. This doesn’t include money invested in lobbying within individual US-states.
Train size increases alone already cause a disproportionate increase in operational risk, with a recent study published in 2024 showing 100-car trains having more than twice the risk of a derailment compared to a 50 car train. And a March 2023 NPR-Article already calculated that the USA currently experiences an average of 3 train derailments per day. They did explain that most of those are low-speed incidents in shunting yards, but even if only a small percentage has severe consequences that is still a lot of severe consequences when one is dealing with around 1000 derailments per year. The FRA, which is meant to regulate rail traffic in the USA and ensure rules and regulations are upheld, is fairly overwhelmed by this point. Back in 2013, the FRA revealed that they have the staff and budget to inspect 1% of the railroad activities falling into their jurisdiction every year. This leaves the railway operators themselves as the primary entity to ensure safe operations, something obviously somewhat handicapped by the fact that the companies also have a commercial perspective and interest which the FRA’s inspectors don’t have. Effectively, the US rail system largely leaves the observation of behavior regarding regulations in the hands of entities who’re not too interested in some of those regulations.

The current situation in the USA is the result of Precision Scheduled Railroading (PSR). PSR was developed as a maximum efficiency strategy in 1993, being pioneered by Mister Harrison who, before his 2017 death, worked as the CEO of 4 major North American Railroads. Mister Harrison was praised as a great strategist, allegedly mapping out train routes in his home and not just cutting big cost factors like closing facilites and laying off staff but also looking towards the most minor avoidable costs like low-usage rail lines being torn out or no longer paying for the hotels train crews slept in if they had an overnight stay. And in a way his approach was obviously successful, reducing cost and maximizing efficiency in such an attractive way that PSR has since become the industry standard and, among other things, is a driving factor behind the escalating train lengths in North America.
A longer freight train can be cheaper, since the costliest part of it is the locomotive, especially the one with the crew in it. The increased length doesn’t just rapidly increase the risk of derailments, but also has off-track consequences. A train that pulls into a siding which was built a few decades ago will now often stretch back onto the main line, not just creating a collision risk with other trains but also possibly blocking level crossings. An FRA-study in 2022 found that that year alone had seen 30799 cases of a parked train blocking a level crossing in the USA, which doesn’t just inconvenience locals and handicaps road-bound freight traffic but has also had severe consequences when parked trains blocked ambulances or firefighters on their way to an emergency. To make matters worse, 958 of the blockages found by the study lasted over 24h, too. There have also been several cases of people who climb through the parked train to cross the tracks being injured or killed when the train started moving unexpectedly. The thought-process behind the idea of climbing through between or under train cars is somewhat understandable, as the length can have the stopped train stretch beyond the horizon on either side.

BNSF, another major US rail operator, caught some negative public feedback when it was revealed that they required workers to schedule sick days 30 days in advance, and that they could only schedule them on Tuesday, Wednesday or Thursday. BNSF ended the practice in fall 2023, likely due to the backlash, but according to unions “go to work sick and tired — or get fired” is still the industry standard.
The combination of reduced staff and increased workloads has also had ripple effects in other parts of railroad operation. The crew members in charge of pre-departure inspections (often, at this point, one person per train), used to have around 7 minutes per train car to check the wheels, brakes and bearings. A former NS-employee told the Wall Street Journal in the aftermath of East Palestine that that time span had gone down to “up to a minute”. The deteriorating standards are supported by a widespread atmosphere of pressure and retaliation regarding safety violations. A former track inspector who had been fired by BNSF sued his employer, in the process publishing a recording of a minutes-long phone call from 2015 where a superior berated him after calling the FRA. Notably, the employee hadn’t actually reported anything in the call, he had asked the FRA-representative a (not further specified) question, but was still told to never contact the FRA for any reason. The firing was eventually concluded to have been retaliation for reporting too many track defects.
This blatant disregard for safety doesn’t come from nothing, as Mister Harrison himself frequently emphasized a “priority list” for railroad operations. The list was led by Service, followed by cost control and asset utilization, with safety coming in fourth place. And it can be argued that, if something is fourth place on a priority list, it’s not really a priority anymore. Harrison himself spoke in front of the Surface Transportation Board in 2017 when he freely admitted to the consequences of his passion project, bluntly saying:
I got blood all over my hands, from injuries in this industry that should’ve been avoidable.

The industry continues to be caught in a tug-of-war between entities who are for stricter regulation and more oversight, while others with at least equal power reject most arguments in favor of improvements in those fields and argue the advantages of the current trend. PSR has made the operation of freight railroads in the US cheaper and thus more profitable, and as advocates will point out the cost for shipping-customers has come down in some cases, but it has also led to (to put it nicely) staffing of questionable sufficiency, which has radically increased the workloads and created a system arguably incapable of keeping up with itself.
Workers have longer hours with less time to do the same tasks, made worse by increased physical strain as something as basic as checking a bearing on the rear car of a train can now require a 4+ mile hike. Oversight is largely left to the companies who are being overseen, with so little control from outside entities that they have little incentive to uphold regulations that they dislike (read: That endanger profits). The FAA can track just about every aircraft flying above the USA at any point, knowing who owns it, where it’s from and where it’s going, along with information about who or what’s in it being easily accessible. The FRA doesn’t even remotely have the same capability, not even being able to accurately track just the trains carrying dangerous cargo. And inspecting just 1% of the industry per year creates not only an industry where unsafe rolling stock or practices can fall through gaping cracks and go unnoticed, they also create a confidence in the companies that they will get away with not paying too much attention to how they should run things if that collides with how they want to run things. This confidence came to an exemplary peak in June 2024, when the NTSB revealed that their employees had been threatened by Norfolk Southern employees during the East Palestine investigation, along with the operator withholding demanded documents and pushing to have questionable evidence they gathered outside the investigation to be included in the report.
In summary, PSR has led to a highly profit-motivated operational culture in North American freight railroading, accepting widely known risks as cost of doing business as those meant to ensure safe operations are motivated to turn a blind eye to issues while independent entities are hopelessly overwhelmed with the task they’re given. Norfolk Southern themselves are a decent example of this, winning an award for operational safety 20 years in a row until the award was discontinued in 2012, only for workers to notice an obvious shift in company culture when the company introduced PSR in 2019. A railway worker summarized the situation and the seemingly only way to actual improvement in a 2021 interview with Vice Media as follows:
“I do think it’s a matter of time. There’s going to be a freight car that hasn’t been inspected in 90,000 miles that comes off the track, as it goes off the track and slams into other cars, into a tank car, and either explodes or leaks poisonous gas out. It’s going to take something like that, and a lot of deaths, and then all of a sudden everybody’s going to care.”
A Norfolk Southern employee supported that statement, stating that they’d seen freight cars pull in after 90 thousand miles (145 thousand kilometers) without an inspection when guidelines demanded no more than 3500 miles (5630 kilometers) between inspections. According to him it’s completely reasonable to expect that several train cars in any given freight train have severe defects from damage or neglect. A given example was the fatal 2018 train collision at Granite Canyon, Wyoming, which was caused by a brake defect on one of the two freight trains. The NTSB had found that 6 out of 10 freight cars added to the train shortly before the accident had been overdue for a brake system inspection by between a few months and two years. The accident, according to the NTSB, could’ve been avoided if all regulations and guidelines had actually been upheld. Union Pacific, the rail operator involved, reacted by stating:
“Union Pacific has recognized many operational efficiencies in the past few years that have reduced the amount of equipment and resources on our network.”
“We found ways to increase efficiency (-> profits) at the cost of sufficient equipment and resources”

Comparisons have been made to the status of the airline industry, where it took a string of plane-crashes within a fairly short time-frame to bring attention to lackluster safety-culture at Boeing, one of the main aircraft manufacturers. The tragedy at Lac-Mégantic, which had claimed over 40 lives and leveled the downtown area, had been too isolated to cause public attention that forces a change. In a way, the (somewhat) lucky coincidence that a lot of the USA’s freight train derailments happen in remote areas also means that public interest in avoiding them is low. The reaction would be different if it would happen more often in populated areas, but that would also obviously make the outcomes far more severe. Both the worker who called a catastrophe a matter of time and the one who had seen the severely neglected freight cars spoke to the press anonymously, by the way, as they feared retaliation for speaking out about a culture that has workers forced to either purposely neglect safety or be responsible and risk punishment for missing required performance numbers. Efficiency means profit, and profit is king.
Sacrifices to be made
This brings us back to East Palestine in particular, and the handling of the wreckage. Norfolk Southern successfully pushed for a questionable (and eventually deemed unnecessary) vent and burn procedure, releasing huge amounts of toxic materials into the environment. This, however, allowed them to clear the wreckage faster than if they had waited to further observe the tank cars, allowing traffic through the site to restart sooner.
Mister J.D. Vance, at the time senator of Ohio, put his view of the events quite bluntly during a senate hearing on the handling of the aftermath in March 2024. In his words, East Palestine was sacrificed. Norfolk Southern supposedly chose to poison the area, contaminate air, soil and water, so freight trains didn’t have to wait or take detours much longer.
“When you have an unnecessary uncontrolled burn that poisoned a lot of people, that then led to the rapid transit of train traffic, a lot of people, including me, are wondering, did they do this not because it was necessary but because it allowed them to move traffic and freight more quickly?”
Residents saw their pets unexpectedly die the night following the controlled burn as far as 16km/10mi away, and people in the area not only reported dealing with symptoms of post-traumatic stress disorder but also continued health-issues related to intoxication from polluted air and water. 25 million gallons (94.6 million liters) of contaminated water and 80 thousand tons of contaminated soil had been removed by summer 2023, with no end in sight and at that point not even a plan for some of the affected creeks. A 2024 analysis found “extreme concentrations” of multiple chemicals, including chloride, and exceptionally high pH-levels not just in East Palestine, but in very slowly decreasing levels over an area of 1.4 Million km², affecting 16 US-states (and likely Canada, where no information was available) long after the accident.
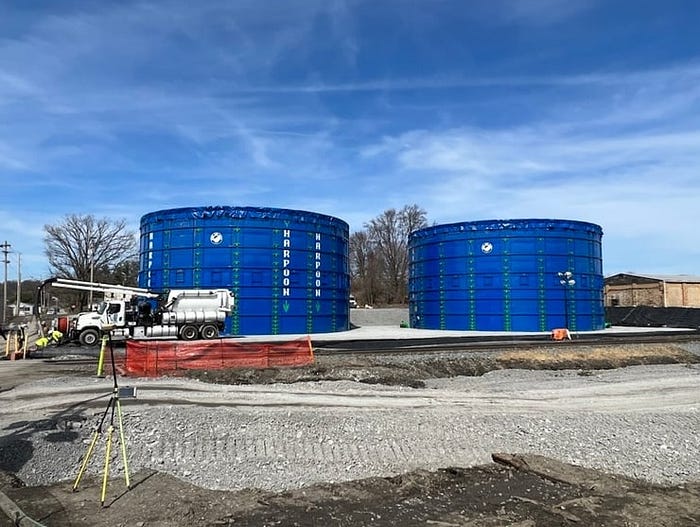
Three class action lawsuits were filed against Norfolk Southern in the aftermath of the accident, which were eventually settled when Norfolk Southern paid 600 million USD (547 million Euros) in total. The settlement saw residents receive up to 25 thousand USD (23 thousand Euros) for health problems and 70 thousand USD (64000 Euros) per household for property damages depending on their proximity to the site, but money was deducted if any aid had already been provided. This meant, for example, that residents who had to relocate and live in hotels or rented spaces paid by the railroad sometimes got nothing. A lot of residents reported that they felt threatened and pressured by the NS’ lawyers, but many of them eventually accepted the settlement, taking the payment they could get at the cost of not being able to sue for damages if they later faced further consequences (like cancer) as the perspective of going up against the railroad alone was considered intimidating. A group of residents did try to challenge the settlement in early 2025, but was told by a judge that they would have to provide an 850 thousand dollar (776 thousand Euros) bond ahead of a possible trial. To compare, the lawyers NS hired to work out the settlement received 162 million USD (148 Million Euros) in fees.
The EPA had largely taken the side of the railroad, explaining that pollution was supposedly below dangerous levels as residents got ill and downplaying reported symptoms. Some accused the EPA of purposely covering up the scale of the problem, claiming that air purity sensors weren’t properly set up (or not turned on) and that the deployment of chemical-scanning aircraft was delayed in an effort to get less bad results. One of the whistleblowers worked on one of those aircraft and reported being instructed to turn off the sensors when flying over contaminated creeks and being routed around certain areas close to the site. The only part that could be sufficiently proven was that the EPA had only deployed the aircraft days after the accident, compared to deployments usually happening within hours of a spill.

As it stands East Palestine was an, as the NTSB put it, 100% avoidable accident caused by a standardized practice which prioritizes profits over safety. The accident currently officially stands at no fatalities and no injuries, but coming years and decades will show how many people the accident actually injured. This is a rail accident which might claim lives over a decade after it happened, and it was painfully avoidable.
Norfolk Southern has promised to improve operational safety after the accident, announcing a review of their operational priorities and “raise the bar” companies in the industry are measured by. The outcry after the accident also led to Norfolk Southern and other major freight railroads announcing that they would join the FRA’s anonymous safety reporting system, but this promise remained empty months after it was made as the railroad explained they wanted to retain the ability for “regular disciplinary action” in certain circumstances. In the end, it’s unclear how much of the promised investments in safety and improvements in company culture will actually become reality.

_______________________________________________________________
The full 216-page report by the NTSB can be found right here.
_______________________________________________________________
I have chosen to stay off Medium’s monetization offers to keep these stories as accessible as possible, but you can support me with a small tip via “Buy me a coffee” if you feel like it.
_______________________________________________________________
A kind reader is posting the installments on reddit for me, I cannot interact with you there but I will read the feedback and corrections. I will link to the post as soon as I can.